FLAT ROOF
SYSTEMS
Built-Up Roof
Systems
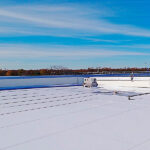
1840
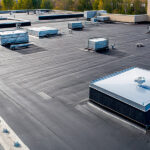
1960
BUR Systems captured more than 90% of the flat roofing market.
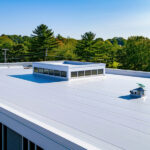
1970
BUR system’s market share declined to 40% of the flat roofing market.
No need for fasteners, which create additional risk of leakage.
But the emergence of other systems, along with a decline in workmanship among BUR practitioners, saw the method’s market share decline in the 1970s to as low as 40 percent.
No need for ballast, which is often laid loose in the form of stones and can be blown off by heavy winds.
Less movement in the form of expansion and contraction, which leads to buckling, ridges and splits
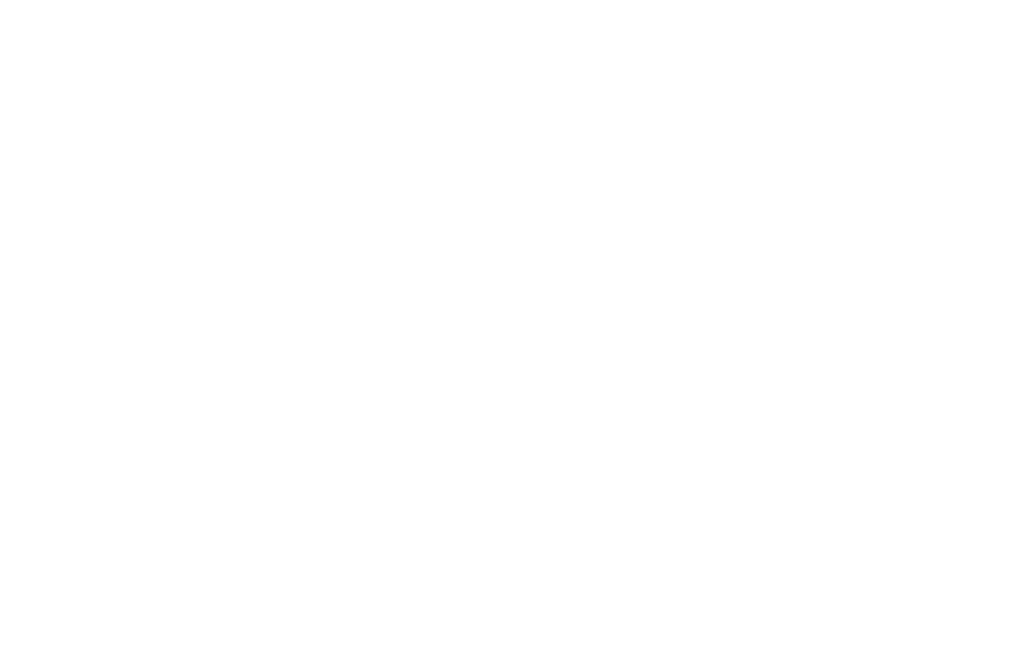
Modified Bitumen
Roof Systems
Modified Bitumen (MB) is asphalt that has had modifiers added to it to give it plastic or rubber-like properties. The most common types of modifiers being used are APP (Atactic Polypropylene) and SBS (Styrene Butadiene Styrene).
Modified Bitumen roof systems consist of one, two, or three ply systems. The type of substrate will often determine the type of system being installed. Modified membranes can also be installed in conjunction with built-up roof materials (such as multiple plies of fiberglass felt) to form a “hybrid” roof system. Modifieds have proven performance on residential, commercial, and industrial applications.
APP Modifieds
In order to create roofing grade asphalt, asphalt flux is air-blown at elevated temperatures which converts the flux to roofing grade asphalt. In the early 1970’s, the Italians, lacking the blowing equipment, were looking for a product that would convert asphalt flux into a usable roofing product. They discovered that if Atactic Polypropylene (APP) – a by-product of propylene polymerization – was added to asphalt then it gave the asphalt some plastic properties. They found that by adding about 30% of APP modifier, they could stretch the modified asphalt up to fifty percent of its original length before it would break.
Next came the need to make it into a usable roll product. Some type of reinforcement would be needed.
They looked into various reinforcement materials and decided on a polyester mat because polyester would accommodate the APP modified asphalt’s elongation properties whereas the more commonly used woven glass mats would not. The reinforcement material is dipped into the hot modified bitumen mix, then goes through a rolling cylinder, cooled, and then wound into a roll.
APP membranes are applied using a torch. The back of the sheet has extra asphalt on it which, when heated, bonds to the substrate. This was especially convenient for the smaller, more cut up roofs because less room and equipment is needed on site to torch-apply a membrane than is necessary for application using hot bitumen.
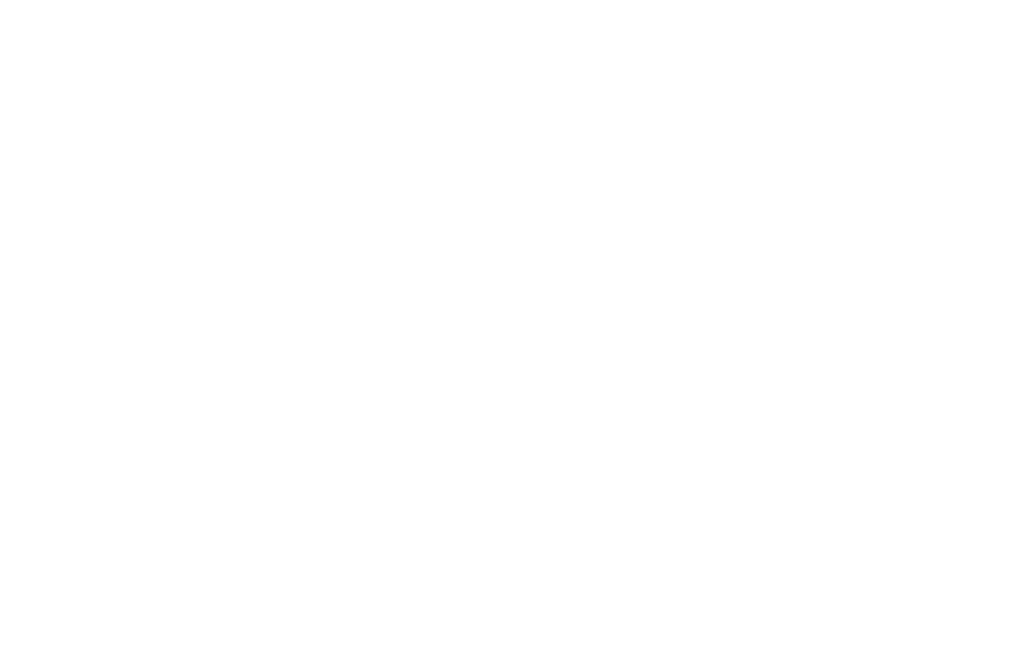
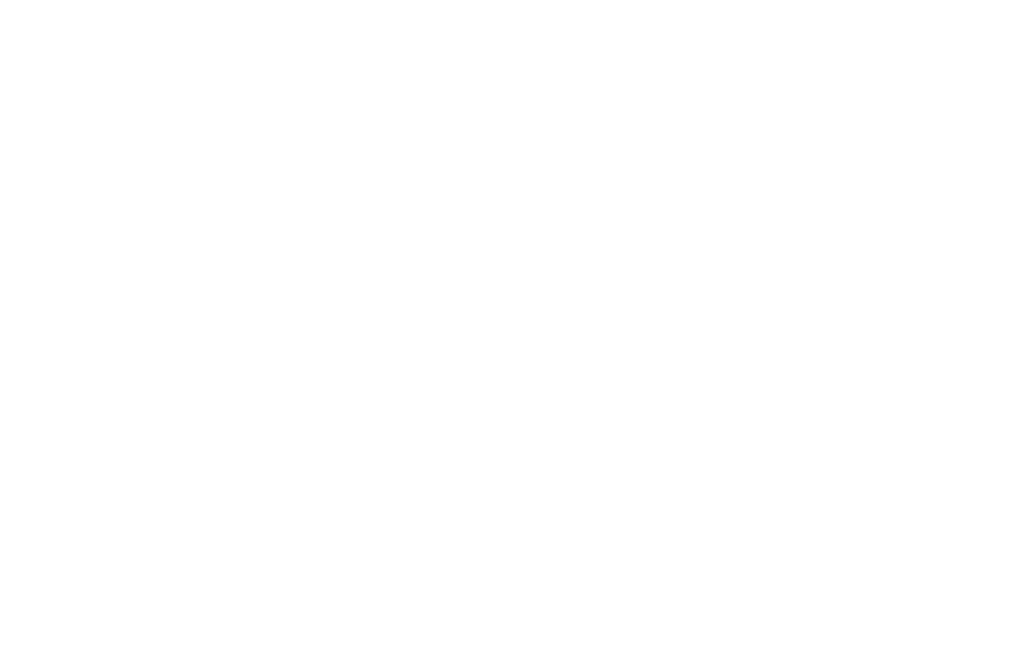
SBS Modifieds
While APP was being looked into in southern Europe, northern Europe was experimenting with a different type of modifier called Styrene Butadiene Styrene (SBS).
The French and Germans found that if they added 10%-15% of SBS rubber to asphalt, the asphalt’s characteristics changed to those of the rubber additive. They learned that they could stretch the SBS modified asphalt up to six times its original length and that, unlike the APP, it would return to its original size when allowed to relax.
There are a wide range of reinforcements used in SBS roofing materials. These include fiberglass or polyester mats and scrims, or combinations of both. The fiberglass mats range in weight from 1.0 to 2.5 pounds per 100 square feet or around 50 to 125 grams per square meter. Polyester reinforcements range in weight from 3.5 to 5.0 pounds per 100 square feet or 170 to 250 grams per square meter. The type of reinforcement used depends on the material’s performance requirements.
Single Ply Roof Systems
Single-Ply roof systems have outstanding UV-ray resistance and extraordinary resistance to weather elements.
Their white reflective and ‘cool roof’ characteristics help reduce a building’s energy costs. The reduction in the surface temperature of the roof reduces the amount of expansion and contraction of the roof deck. Single-ply membranes also provide the ability to cover very large areas more economically.
Single-ply roof systems are based on several types of products; generally TPO (thermoplastic polyolefin), PVC (polyvinyl chloride) and EPDM (ethylene propylene diene M-class rubber). These are membrane products that are factory fabricated and installed in the field as a single layer. Single ply roofing systems can be loose-laid (ballasted), adhered, or mechanically attached to the roof deck. The seams of these systems are either hot-air welded or chemically bonded at the seams.
Single-ply roofing systems offer ease of installation, lighter material weight, and a lower relative labor cost on larger projects. The membranes used have outstanding longevity characteristics and come with some of the longer manufacturer warranties in the roofing industry.
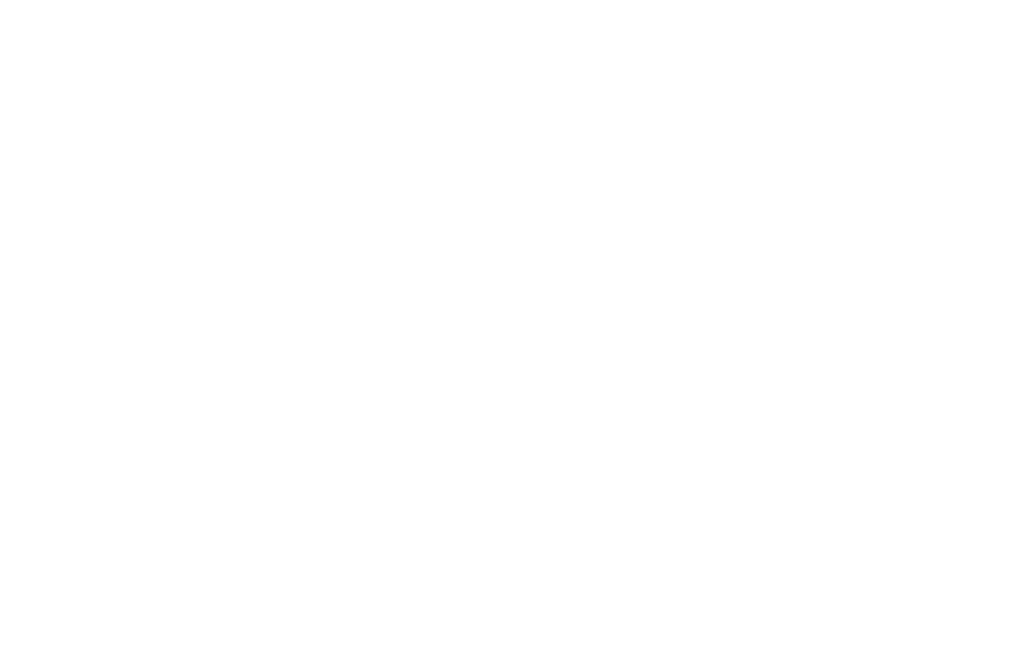
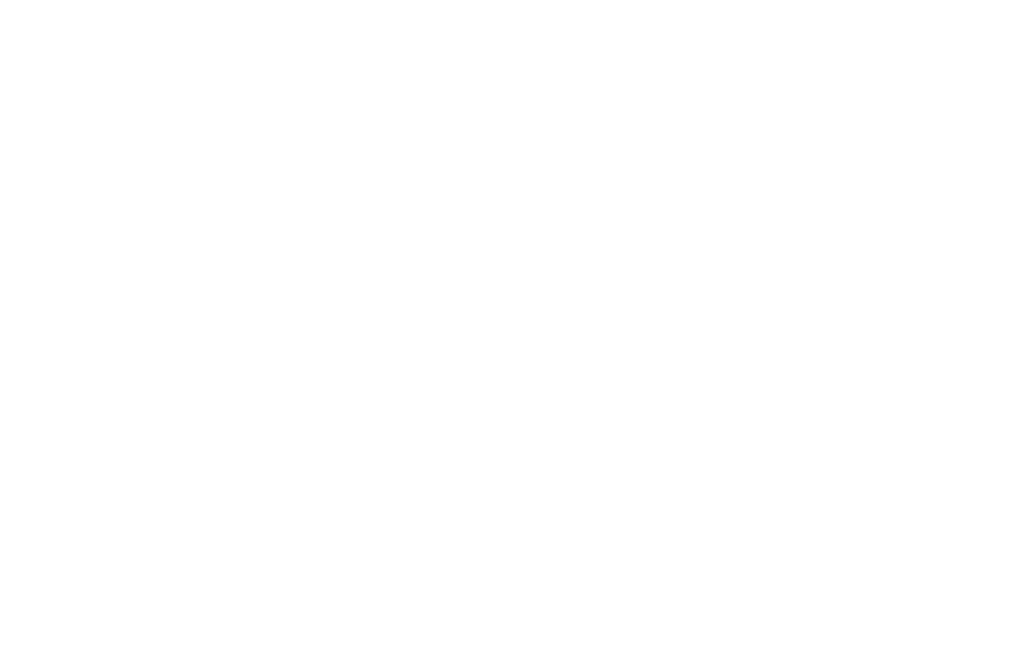
Commercial services
The risks of shortcutting any of these factors are too high to ignore and often lead to costly, premature roof failure…
Residential Roofing
Repair Services
One of the most important steps in achieving this goal, yet the most overlooked in many organizations, is roof maintenance and repairs…
Our Clients in The State of florida say:
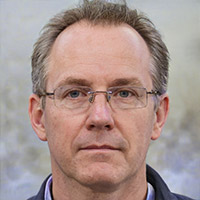
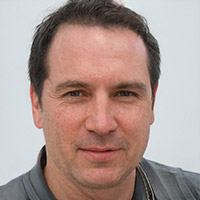
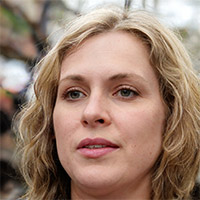
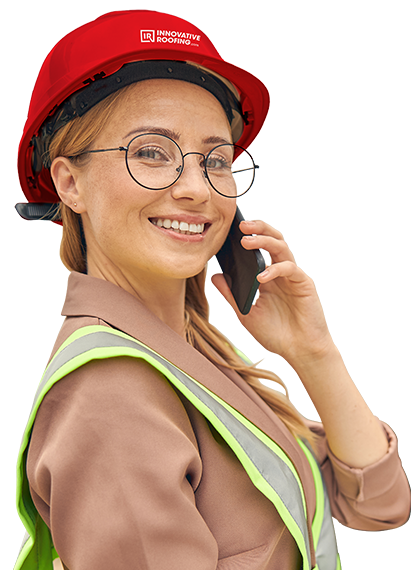